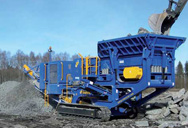
Feed Size On The Ball Product Ball Mill - bio-medi.de
Feed Size On The Ball Product Ball Mill. Production capacity : 0.65-615t/h . Feeding Size : ≤25mm . Discharging Size : 0.075-0.89mm. Mineral Processing Equipment: feed size on the ball product ball mill - A type of mining equipment that can trigger the development and change of the beneficiation technology industry.The main core machines are ball mills, rod mills, flotation machines ...
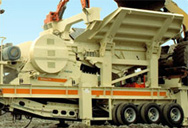
Ball Mills - Mineral Processing & Metallurgy
Difference Between a Rod Mill and Ball Mill. Rod Mills has a very define and narrow discharge product size range. Feeding a Rod Mill finer rocks will greatly impact its tonnage while not significantly affect its discharge product sizes. The 3.5” diameter rod of a mill, can only grind so fine.
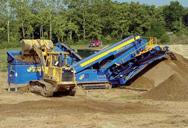
Optimum choice of the make-up ball sizes for …
However, as a group, they are not entirely satisfactory because the optimum mixture of balls depends on the feed size as well as the product size. Further, the ball size distribution in the mill is not a simple parameter that can be controlled directly, as it depends on the make-up ball charge and wear rate.
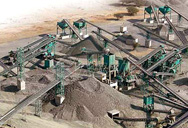
Calculate and Select Ball Mill Ball Size for Optimum …
In Grinding, selecting (calculate) the correct or optimum ball size that allows for the best and optimum/ideal or target grind size to be achieved by your ball mill is an important thing for a Mineral Processing Engineer AKA Metallurgist to do. Often, the ball used in ball mills is oversize “just in case”. Well, this safety factor can cost you much in recovery and/or mill liner wear and ...
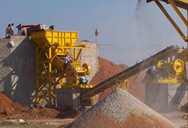
ball mill product size distribution
Ball Mill Power Calculation Example 1 A wet grinding ball mill in closed circuit is to be fed 100 TPH of a material with a work index of 15 and a size distribution of 80 passing inch 6350 microns The required product size distribution is to be 80 passing 100 mesh 149 microns.
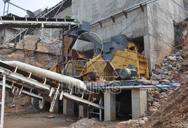
Ball Mill - RETSCH - powerful grinding and …
RETSCH is the world leading manufacturer of laboratory ball mills and offers the perfect product for each application. The High Energy Ball Mill E max and MM 500 were developed for grinding with the highest energy input. The innovative design of both, the mills and the grinding jars, allows for continuous grinding down to the nano range in the shortest amount of time - with only minor warming ...
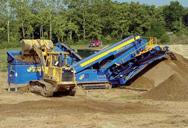
Ball mill - Wikipedia
A ball mill is a type of grinder used to grind, blend and sometimes for mixing of materials for use in mineral dressing processes, paints, pyrotechnics, ceramics, and selective laser sintering.It works on the principle of impact and attrition: size reduction is done by impact as the balls drop from near the top of the shell. A ball mill consists of a hollow cylindrical shell rotati
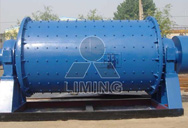
Mill (grinding) - Wikipedia
F 80 is the mill circuit feed size in micrometers. Rod mill. A rotating drum causes friction and attrition between steel rods and ore particles. [citation needed] But note that the term rod mill is also used as a synonym for a slitting mill, which makes rods of iron or other metal. Rod mills are less common than ball mills for grinding ...
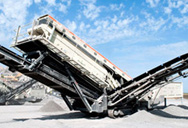
Ball Mills - an overview | ScienceDirect Topics
where d b.max is the maximum size of feed (mm); σ is compression strength (MPa); E is modulus of elasticity (MPa); ρb is density of material of balls (kg/m 3); D is inner diameter of the mill body (m).. Generally, a maximum allowed ball size is situated in the range from D /18 to D/24.. The degree of filling the mill with balls also influences productivity of the mill and milling efficiency.
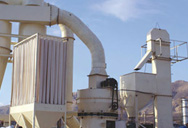
Ball mills - liming
First, a Jar Mill grindability test requires a 5 lb. (2 kg) sample and produces a direct measured specific energy (net Hp-hr/t) to grind from the design feed size to the required product size. The second test, a Bond Work Index determination, results in a specific energy value (net Hp-hr/t) from an empirical formula.
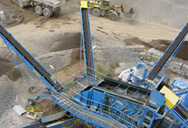
size product ball mill gold ore - joniatuinen.be
product size distribution for a ball mill. Cone Crusher Feed Size Mobile Crusher Manufacturer. 3.The gap between the rollers is adjustable, so the output size and capacity would be changed accordingly.4.This crusher adopts unpowered distributor, the materials will be evenly distributed into the crusher to ensure good output size and protect the roller surface from being worn down unevenly.5 ...
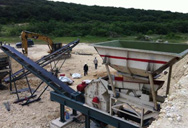
Ball Mill: Operating principles, components, Uses ...
A ball mill also known as pebble mill or tumbling mill is a milling machine that consists of a hallow cylinder containing balls; mounted on a metallic frame such that it can be rotated along its longitudinal axis. The balls which could be of different diameter occupy 30 – 50 % of the mill volume and its size depends on the feed and mill size.

specifications of balls of a ball mill product size
steel ball production mill - friesenhaus … Ball Mills Steel Ball Mills & Lined Ball Mills. Particle size reduction of materials in a ball mill with the presence of metallic balls or other media dates back to the late 1800s. The basic construction of a ball mill is a cylindrical container with journals at its axis.
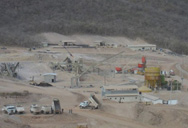
applications of ball mill - cannonb.ru
A ball mill also known as pebble mill or tumbling mill is a milling machine that consists of a hallow cylinder containing balls mounted on a metallic frame such that it can be rotated along its longitudinal axis The balls which could be of different diameter occupy 30 50 of the mill volume and its size depends on the feed and mill size ...

Effect of ball and feed particle size distribution on …
It was also observed from the experimental results that in order to increase the milling efficiency of a ball mill, towards optimum production of material in the desired size class, there is a need to correlate the ball size and the feed size distributions.
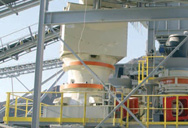
Optimization of mill performance by using
Optimization of mill performance by using online ball and pulp measurements Soon after a stop, a mill is a dangerous place to enter for the personnel tasked with taking measurements or samples. Crash stops are difficult to handle. The mill and all feed streams should be stopped simultaneously but, often, they are stopped around about the same time.