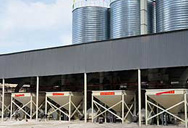
How to Choose Gold Smelting Flux - Superb …
Gold smelting flux helps us to take advantage of this fact in the smelting process. Flux is able to react only with the impure metals, thereby causing them to form nitrates which can separate out neatly. Again, smelting flux makes metallic oxides easy to eliminate, thereby removing another major source of impurity. This goes a long way in making the smelting process more efficient. Ensuring ...
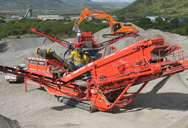
Processing, smelting and refining gold | World …
Processing, smelting and refining gold. From ore to doré . Cyanidation. More gold is recovered by cyanidation than by any other process. In cyanidation, metallic gold is oxidised and dissolved in an alkaline cyanide solution. When gold dissolution is complete, the gold-bearing solution is separated from the solids. With ores of higher gold content (greater than 20 grams of gold per tonne of ...

Smelting and Gold Refining Part 1: Smelting …
17.08.2015 · Smelting and Gold Refining Part 3: Recovering the Gold From Anode Slimes! ... Gold Recovery via Copper Electrolysis - Part 1 - Duration: 33:54. Successful Engineer 52,980 views. 33:54 . Twelve ...

Smelting and Gold Refining Part 3: Recovering …
23.11.2015 · Secondly, by direct smelting the handling is greatly reduced, ie take your shaker table cons, mix them with some flux and collector metal and smelt, pour your product. Now I should also mention ...
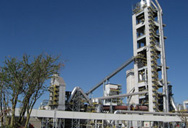
Smelting vs. Electrolysis
Smelting vs. Electrolysis Difference Between Smelting And Electrolysis . Smelting is the final process that provides the metal in a pure enough form for machining and fabrication. This process entails heating the ore to fuse the metals together and refining it by removing the sulfur and other volatile materials and impurities. Smelting processes vary with the metal and according to the type of ...
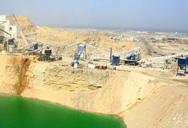
(PDF) The application of direct smelting of gold ...
A study by Amankwah, et al., (2010) on the application of direct smelting of gold concentrates as an alternative to mercury amalgamation showed that the direct smelting methods yields 99.8 % ...
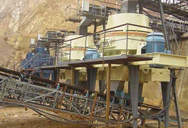
Direct smelting method - LinkedIn SlideShare
DIRECT SMELTINGMethod Equipment/ Principle Applicability ProcessChemical Direct Smelting Melting black Smelting is applied in most small sand scale centres and miners are familiar concentrates to with the method as it is being used produce pure for purifying sponge gold. It has been gold developed, tested and commercialised in Ghana. It can be use for all types of ores and comparatively ...
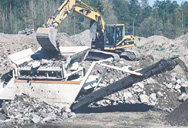
Electrowinning and Smelting - Resource Book
Gold Smelting Purpose of Smelting Smelting is the final stage in the production of tile gold. The purpose of smelting is to remove the metallic and other impurities into the slag phase, and produce a gold-silver bullion containing typically >95% precious metals. The smelted product, called dore bullion, is unsuitable for direct sale and is hence sent to a refinery for further processing to ...
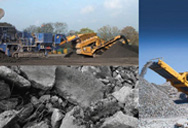
A Poor Mans Method of Smelting Gold | Sciencing
Smelting gold usually involves high-tech and high-cost tools to perform. Mostly, mining companies do the procedure, which sees one material bonded to or released from another in the presence of extreme heat. However, prospectors, and people at home, can smelt their old gold using some simple steps. All it requires is access to a few common minerals and compounds, and a high heat source ...

Guidelines on flux calculation gold smelting - …
SMELTING GOLD FROM STEEL WOOL CATHODES. This discussion comprises an early draft for my contribution to: Trainor D & D Menne [1990]. The pyrometallurgy of gold refining. Pyrometallurgy Seminar. 9 November, Murdoch University, Perth, Western Australia, pages 155 to 183. THE DIRECT SMELTING OF DORe-LOADED STEEL WOOL CATHODES. D Menne, Consulting Metallurgist, 14 …
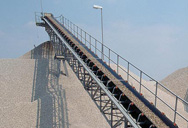
Difference between gold smelting equipment & …
Gold smelting. First, gold smelting require specialized equipment – furnace, chemicals, mold and source of heat. As I stated earlier, this process aims to produce pure gold (free from impurities). To achieve this, you need to: Pulverize gold material into fine pieces; Heat the furnace to temperature between 1150 and 1450 ̊C ; Place gold ore to burn off impurities; Introduce chemicals to ...

Outotec Direct Zinc Melting Process - Outotec
The Outotec® Direct Zinc Smelting (DZS) process provides a means for the direct pyrometallurgical treatment of zinc sulphide concentrates to produce a high-purity, oxide fume and low zinc content discard slag. The process is particularly well suited to the processing of low-grade concentrates with significant concentrations of gangue impurities such as SiO2, CaO and MgO, thereby overcoming ...
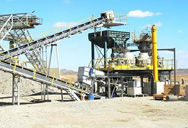
Gold Smelting - OpenLearn - Open University
Gold Smelting . Updated Tuesday, 27th February 2007 . The process of smelting gold, one of the scientists challenges on the BBC/OU series Rough Science 3. This page was published over five years ago. Please be aware that the information provided on this page may be out of date, or otherwise inaccurate due to the passage of time. For more detail, see our Archive and Deletion Policy. The ...
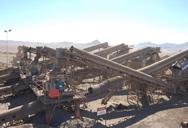
(PDF) Enriching gold from refractory gold …
These smelting processes could be divided into two kinds, namely, indirect smelting and direct smelting. In the indirect smelting process, the calcine of refractory gold ores are added in the ...
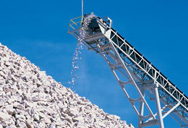
What is smelting? What is electrolysis? | Yahoo …
28.04.2009 · Smelting: The act of melting something like a metal, possibly to improve it. Electrolysis: This is running electricity through a liquid (i.e.,water) and separating it into what its made of. (water is 2 parts Hydrogen, 1 part Oxygen.) This is usually performed in what is called an "electrolysis chamber". This looks like 2 vertical tubes in a ...
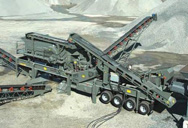
Electronic Scrap Precious Metals Recovery: Gold, …
A process comprising incineration, caustic leaching to remove aluminum, smelting with a siliceous slag, and electrolysis recovered 99.9 percent-pure copper metal and anode slimes assaying more than 7,000 ounces per ton of combined precious metals. Silver, gold, and copper recoveries were 93, 95, and 87 percent, respectively. Cost analysis indicated that an alternative process using direct ...
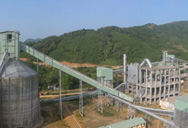
Gold Steel Wool Cathode Smelting-Henan …
Gold Steel Wool Cathode Smelting. Environmental protection Energy-saving Low cost. 2018 3 6gold is recovered from the pregnant strip solution by electrowinning onto steel wool. the gold depleted calcining the steel wool cathodes and direct smelting more detailed. gold mineral fact sheets australian mines atlas depositing the gold on a steel wool cathode. ready for smelting..Cathode frame ...
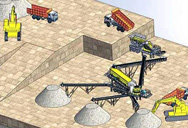
Direct smelting | metallurgy | Britannica
Other articles where Direct smelting is discussed: lead processing: Direct smelting: Indirect smelting in roasters and blast furnaces began to be replaced in the 1970s by several direct smelting processes conducted in relatively small, intensive reactors. These processes require neither the sintering of feed materials nor the use of metallurgical coke; also, they produce…
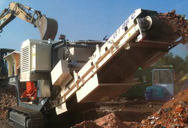
Difference between Melting and Smelting | …
Smelting is done for basic metals like iron, copper, silver and gold. Chemicals such as reducing agents are used to wash out other elements from ores into gases or slag (waste); this leaves just the metal behind. Carbon is the most commonly used reducing agent. While producing metals, two most important forms used as reducing agents are carbon monoxide and carbon dioxide. Most of the ores are ...