
processes and purification of iron ore locally
Höganäs sponge-iron process and the water-atomizing process. The former process is based on reduction of iron ore, yielding a highly porous sponge-iron which subsequently is comminuted to powder. The latter process is based on atomization of a stream of liquid iron (or steel) by means of a jet of pressurized water. Both processes will be...
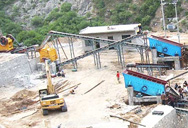
processes and purification of iron ore locally
Iron ore is converted into various types of iron through several process The most common process is the use of a blast furnace to produce pig iron which is about 92-94% iron and 3-5% carbon with smaller amounts of other elements...
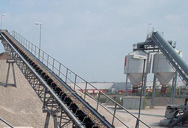
Iron processing | Britannica
Throughout the 20th century, many new iron-making processes were proposed, but it was not until the 1950s that potential substitutes for the blast furnace emerged. Direct reduction, in which iron ores are reduced at temperatures below the metal’s melting point, had its origin in such experiments as the Wiberg-Soderfors process introduced in Sweden in 1952 and the HyL process introduced in Mexico …
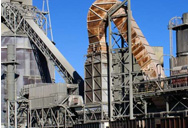
The Six Main Steps of Iron Ore Processing | …
When the iron ore is extracted from the mine, it must undergo several processing stages. Six steps to process iron ore. 1. Screening. We recommend that you begin by screening the iron ore to separate fine particles below the crusher’s CSS before the crushing stage. A static screen is used to divert the fine particles for crushing. This step prevents overloading the crusher and increases its efficiency.

processes and purification of iron ore locally
Metal Ore Extraction and Processing - Springer Link. The industrial sequence diagram for the metal ore extraction and processing ... not have to be dealt with, and local vegetation and habitat suffers minimal .... in Figure 10.3, with the injection of iron ore pellets, crushed lilimingne, and coke.

Processes and Procedures in the Extraction of Iron ...
The extraction of iron from its ores is quite a technical process. The iron ore is first roasted in air to produce iron(III) oxide which is mixed with coke and limestone and then further heated to a very high temperature in a blast furnace. These materials are loaded into the blast furnace from the top while a blast of hot air is introduced into it from beneath via small pipes known as tuyeres. The …
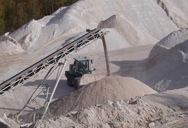
PURIFICATION OF IRON ORE (BY MAGNETIC …
The Ore of Iron can easily be separated from Gangue by this method. Large amount of ore can be purified by this method. It has two rollers, one is magnetic roller & other one is nonmagnetic roller. When ore is dropped on the magnetic roller, it moves through conveyers and it flows from the magnetic roller. The magnetic roller attracts magnetic ore from the main ore and the waste ore is …

Iron Ore Beneficiation Process - …
Iron Ore Beneficiation Process. Previous Next View Larger Image; During the last ten years great strides have been made, on the Mesabi range, in the practice of beneficiating low grade iron ore material. By beneficiation is meant all methods of removing impurities, and raising the iron content to a point where it can be sold in open market, the principal impurities being silica and moisture ...
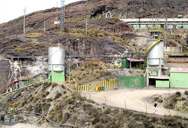
Purification Of Iron Ore In A Blast Furnace
Patent US3454395 - Process for the reduction of iron ore in… In more particular, the invention is based upon the ability to reduce iron or to a Generically, a blast furnace can do what a cupola does but a cupola cannot do. Obtén detalles. Iron & steel - British Lime Association (BLA) part of… The heat in the blast furnace decomposes the limestone to lime, which then reacts with melted and ...
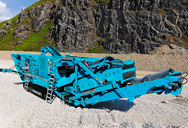
Refining (metallurgy) - Wikipedia
In metallurgy, refining consists of purifying an impure metal. It is to be distinguished from other processes such as smelting and calcining in that those two involve a stone change to the raw material, whereas in refining, the final material is usually identical chemically to the original one, only it is purer. The processes used are of many types, including pyrometallurgical and hydrometallurgical techniques.
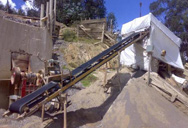
The Extraction of Iron - Chemistry LibreTexts
Iron ore is not pure iron oxide - it also contains an assortment of rocky material that would not melt at the temperature of the furnace, and would eventually clog it up. The limestone is added to convert this into slag which melts and runs to the bottom. The heat of the furnace decomposes the limestone to give calcium oxide. \[ CaCO_3 \rightarrow CaO + CO_2 \tag{5}\] This is an endothermic ...