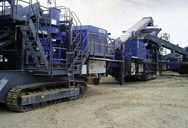
A first survey of grinding with high-compression …
A first survey of grinding with high-compression roller mills. Int. J. Miner. Process., 22: 401-412. The special feature of high-compression roller mills (HC-roller mills) is that a bed of particles is compressed between two rollers to a high solid density more than 70% of volume. The size reduction occurs by interparticle crushing. The milling force must be adjusted to a level so that the particle bed is loaded …
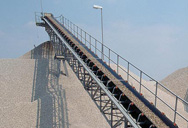
A first survey of grinding with high-compression …
The special feature of high-compression roller mills (HC-roller mills) is that a bed of particles is compressed between two rollers to a high solid density more than 70% of volume. The size reduction occurs by interparticle crushing. The milling force must be adjusted to a level so that the particle bed is loaded by a compressive force per unit area exceeding at least 50 N/mm
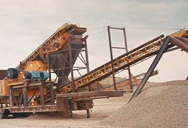
New Generation of Grinding Media Separation in …
A First Survey of Grinding with a High-Compression Roller Mill. April 1988 · International Journal of Mineral Processing. Klaus Schönert; The special feature of high-compression roller mills (HC ...

Quantifying the energy efficiency of fine grinding ...
Hukki, R.T., Allenius, H., 1968. A quantitative investigation of the closed grinding circuit. Society of Mining Engineers, AIME, Transactions 241, 482-488. Schönert, K., 1988. A first survey of grinding with high-compression roller mills. International Journal of Mineral Processing 22, 401-412. Palaniandy, S., Halomoan, R., Ishikawa, H., 2018. Shifting the comminution workload from the primary ball mill to …
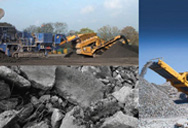
Selection and operation of high pressure grinding …
Fuerstenau, D.W., Kapur, P.C. & Gutsche, O., Comminution of minerals in a laboratory-size, choke-fed high-pressure roll mill. XVIII International Mineral Processing Congress, Sydney, 175 (1993). Schonert, K., A first survey of grinding with high-compression roller mills. International Journal of Mineral Processing, 22, 401 (1988). Kapur, P.C., Sudhir, G.S. & Fuerstenau, D.W., Grinding of heterogeneous …
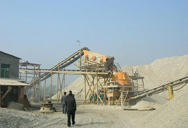
survey of surface grinder - Practical Machinist
19.05.2020 · survey of surface grinder; Likes: 8. Post #3546614 ; Post #3548677 ; Post #3546208 ... being high in the middle by maybe 0.0002" traverse wise. this was measured with a 400 mm beveled straight edge (din 00) using the light gap method and also a 0.0002" shim (pull test). should i scrape that out? 2. the traverse ways are worn convex. this makes sence. as i dont have a parallel of the lenght …
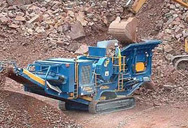
Principles of Grinding | SpringerLink
There are many types of grinding: “precision” and “rough,” internal, external, surface, centerless; using wheels or belts; and conventional or “super” abrasives. I believe they all act the same. When a moving abrasive surface contacts a workpiece, if the force is high enough, material will be removed from the part and the abrasive surface will wear. Those two things will always ...
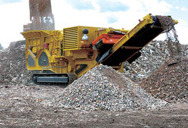
A survey of recent grinding wheel topography …
1. Introduction. The modern grinding process of forming materials has existed for over a millennium, stretching back to water-driven stone wheels; however, as an engineered manufacturing process, it was not until the mid-1940s that grinding was scientifically examined and fledgling mechanics were first applied .Much research in the past half-century has significantly advanced the field, and ...
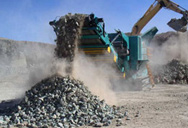
12-18-06 Maximizing the Grinding Process
requests for grinding in angstroms (Å = 10-10 meter or, 0.0039 micro inch) before “kiss” lapping. With process controls demanding “six-sigma” the demand for tighter tolerances will only get more demanding. Spindle Integrity (Balance & Run-Out) Balance and run-out of the grinding wheel are mechanical properties that must be addressed at the time of each grinding wheel mounting ...
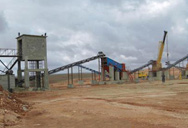
Comparison of low-grade hematite product …
01.05.2012 · The characteristics of comminuted hematite products using a high pressure grinding roller (HPGR) and conventional jaw crusher (JC) were comparatively studied by screening, optical microscope, scanning electron microscope (SEM) and Brunauer, Emmett and Teller (BET) techniques. Major properties investigated included product size distribution, particle cracks, specific surface areas and …
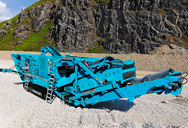
Precision Internal ID Grinding - Grindal Company
Okamoto IGM-2M High Volume Precision ID Grinding Machine. In addition to our 2EF’s cylindrical grinders, we also have Okamoto precision grinding machines. For example, we have an Okamoto IGM-2M for higher volume orders that only require one I.D. ground. This machine has a rigid design that stands up to rigorous high-volume production. Precision Grinding Services that Fit Your Precision ...
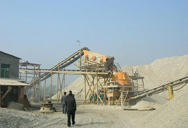
Building the Business Case for Machine Tool ... - …
In our Grinding Automation survey, Service/Support ranked second, behind only Quality, as the most important factor in taking the first step to investing in new automation capability. Having an experienced partner with seasoned application engineers and a reputation for stellar customer service is crucial as you plan your automation investment.
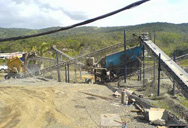
Integral Grinding Hpgr
First Choice For Hpgr Technology And Service. Industries the application of hpgr ranges from coarse grinding eg the grinding of 65mm 25 size excess pebbles in ag circulation loops to final grinding of 100m material to high blaine values in the preparation of pellet feed khd has a history of successfully installed hpgr units which have demonstrated long term reliability and.